Industrial Dryer Control Utilizing Exhaust Gas Humidity
There are various industrial dryers utilized in production facilities. The dryers include spray dryers, flash dryers, rotary (both steam and direct fired), conveyor dryers and many others. Most of these dryers are typically controlled using the exhaust gas temperature as a set point and then control the inlet temperature or feed rate to keep the set point constant. Industry uses exhaust temperature sensors as surrogates to product moisture sensors or exhaust humidity sensors.
The advantage of real time product moisture sensors is that they provide the actual water content of the product being dried so no correlations need to be made from other parameters to determine the product moisture content. One issue with product sensors is that they have a lag in the control for dryers with long drying residence times like conveyor and rotary dryers. The other issue with product sensors is that they have issues with maintenance and accuracy in certain dryer configurations.
The advantages of an accurate, reliable exhaust humidity sensor (H2OOP sensor) are that they don’t have the lag in control of long residence time dryers since the air flow moves through the dryer quickly and they don’t have maintenance and accuracy issues in the exhaust gas.
Below we are going to breakdown how to implement humidity as part of the control scheme for different types of dryers.
Spray Dryers
Spray drying involves atomizing a slurry into droplets that are dried into individual particles in a hot gaseous drying medium. It is a one-step drying process with a very quick residence time. It is used in drying many different products including milk powders, baby formula, kaolin, PVC, detergents, maltodextrin, pharmaceuticals, eggs, yeast and many other products. Figure 1 below depicts a typical spray drying process.
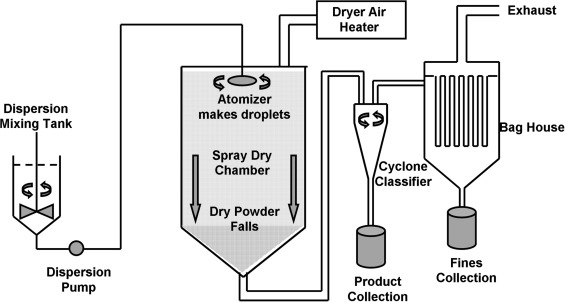
Most spray dryers are controlled with outlet temperature as the setpoint and that varies either the feed rate or the inlet temperature applied to the product. The most efficient way to operate a spray dryer is to maximize the inlet temperature and hold it constant and vary the feed rate. This control will maximize capacity and be more efficient since products release moisture easier at the higher temperatures and it is not a linear relationship.
The other control scenario includes outlet temperature controlling the inlet temperature and holding the feed rate constant. This control scenario is used if particle size control is required. Keeping constant pressure in the atomizer keeps the particle size constant. This control is also used if the upstream feed system has production limitations and can’t keep up at high inlet temperatures.
Product Moisture Control
For adiabatic dryers such as spray dryers, the end product moisture (Xp) has a strong relationship with the inlet temperature (Ti), outlet temperature (To) and the wet bulb temperature (Tw) based on the following equation found in Arun Mujumdar’s 2006 version of the “Handbook of Industrial Drying”:
Xp=K ln ((Ti-Tw)/(To-Tw))
In the past, dryer providers have not included an exhaust humidity sensor as part of the control program due to reliability issues. H2OOP can provide a reliable wet bulb temperature measurement and because of that the product moisture variation is reduced. The following equation can be implemented for control using K, To and Tw as inputs to control the inlet temperature and reduce product moisture variation:
Ti=K(To-Tw) + Tw
The K value will have to be determined from data for each product run on a specific dryer but once established it is repeatable.
Accounting for Ambient Humidity
In some spray dryer applications, the inlet temperature has limitations due to deterioration issues of the product like milk powders, pharmaceuticals and other food products. In these lower temperature applications, the ambient air humidity has a large effect on the drying capacity due to a smaller vapor pressure differential between the process gas and the product.
By implementing an exhaust gas humidity sensor, the dryer control now accounts for the ambient air humidity changes to optimize performance year-round. Outlet temperature control alone cannot detect the ambient changes which causes higher variation in product moisture and can also lead to higher rate of build-up in the dryer.
Product Build-Up
Product buildup in the dryer is an issue for many spray dryers. Build-up has a direct correlation to exhaust gas relative humidity. By knowing the threshold relative humidity for a problem build-up spot in the dryer, you can reduce the rate of build-up and downtime. The best way to establish the relative humidity threshold point is by attaching a temperature sensor on the outside of the duct where build-up occurs. When the dryer is clean, the duct temperature and the process temperature should be close. As you start to see a delta between the two, buildup is happening and the relative humidity value is determined.
Relative Humidity Control
Relative humidity control can also be implemented for product moisture control in applications with constant inlet temperature and feed rate manipulation. The relative humidity tracks the product moisture closely in this control scenario. Relative humidity control accounts for changes in ambient humidity and also can be used for build-up control at the same time if build-up is a limiting factor on the dryer capacity.
Baghouse and Condensation Protection
The final advantage of implementing an exhaust gas humidity sensor is to know the dewpoint temperature prior to a baghouse so the bags don’t blind. The dewpoint temperature will be programmed into the DCS or PLC and an approach to dewpoint (To-DP) can be displayed for the operator on their control screen.
Flash Dryers
Flash drying involves exposing product to high velocity heated gas via screw feeders or paddle blenders. Flash dryers are very useful in removing surface moisture and have a short residence time. Flash dryers are used in all different industries and are frequently found at corn wet milling plants for starches and glutens.
These are also adiabatic dryers and the product moisture correlation equations above also apply for flash dryers. The wet bulb temperature is very important in dryers just removing surface moisture because the wet bulb temperature (adiabatic saturation temperature) is the same as the product surface temperature. Below is a schematic for ring type flash dryer.
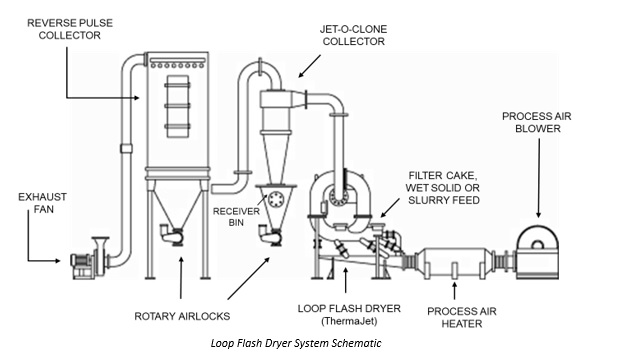
Rotary Dryers
Rotary drying involves a cylindrical rotating shell, slightly inclined, and the feed is introduced at the high end and progresses through the cylinder and is discharged at the bottom end. Rotary dryers have a longer product residence time. There are direct fired and steam tubed dryers. Direct fired utilize combustion to heat the drying air circulated through the dryer. Steam tube dryers are conductive dryers and the walls of the dryer are heated and evaporation occurs when the product is in contact with the walls. The dryers are designed with internal flights to assure the product is well mixed and exposed to the process gas or dryer walls.
Direct fired dryers are typically controlled using the outlet temperature and varying the inlet or burner temperature. Some also have air flow control which is important.
Steam tube dryers are controlled using the exhaust temperature and adjusting the steam pressure which increases or decreases the surface temperature of the dryer walls. These also should have air flow control.
Direct Fired Rotary Dryers
Direct fired dryers can be very efficient if also recirculating part of the exhaust gas as seen in the figure below.
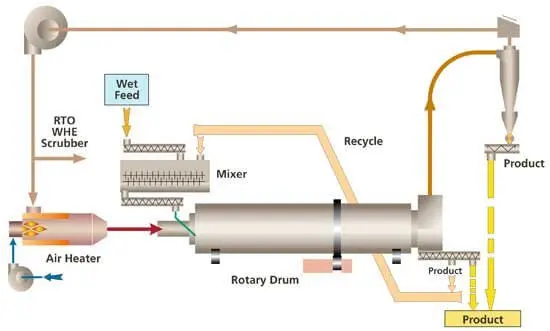
Direct fired rotary dryers need to heat up a lot of air to achieve drying so if you can recycle the exhaust gas, which has a higher temperature than ambient, they become more efficient. In a single pass dryer without exhaust gas recycling, it is important to control the exhaust gas humidity to optimize energy usage as well as improve dryer control moisture. By installing the exhaust gas humidity sensor and controlling to a fixed humidity ratio (lb of h2O/lb of dry air), you can quickly adapt to changes in the feed moisture because the air flow is much quicker through the dryer. The best control scheme is to control the inlet temperature via the outlet temperature and the humidity ratio via air flow control. This allows the dryer to have the right amount of drying air without wasting energy. It also reduces product moisture variation.
The dewpoint temperature of the exhaust gas should also be programmed into the DCS or PLC system of the dryer to protect baghouses from blinding or build-up within cyclones.
For exhaust gas recycle applications, the sensor controls the amount of exhaust gas recycled to optimize energy and also reduce product moisture variation.
Steam Tube Dryers
For steam tube dryers, the air flow is much less but the moisture has to be removed or the evaporation rate will be affected. Typical control for steam tube dryers is outlet temperature controlling the steam pressure and humidity ratio controlling the air flow.
Another advantage of an exhaust humidity sensor will also detect early steam tube leaks so scheduled maintenance can be made and avoid an unplanned shutdown. Below is a typical steam tube dryer configuration:
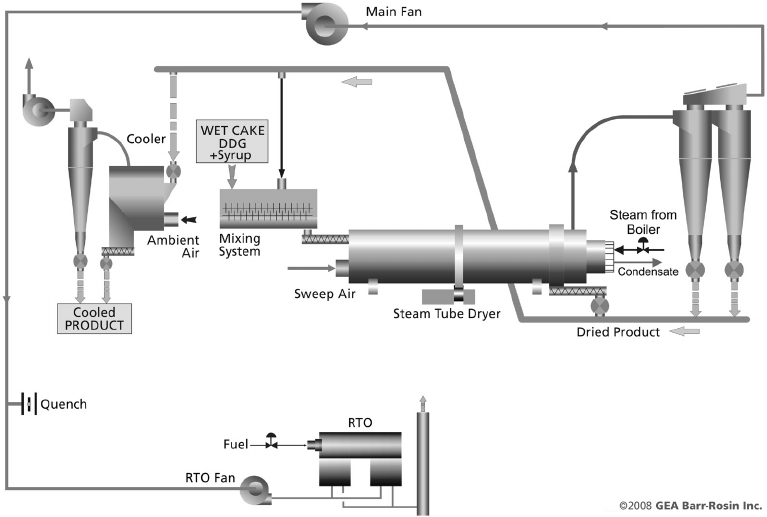
Conveyor Dryers
Conveyor dryers consists of introducing product on a conveyor and forcing hot air through the product bed. They can be single pass or multiple pass applications. Many conveyor dryers have multiple zones and the product has a long residence time. Below is a picture of a single pass conveyor dryer / oven:
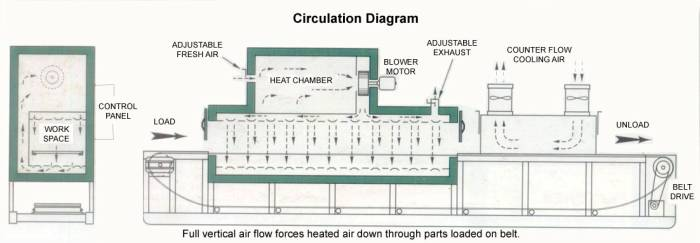
Typical control of conveyor dryers consists of zone temperature control. The air temperature in each zone is controlled and product samples are taken and modifications are made if needed. Most dryers have a controllable exhaust air system. By utilizing humidity ratio control, you optimize energy and provide a more consistent drying environment in each zone.
Another advantage is by knowing the wet bulb temperature in each zone, you can also determine when free moisture is no longer available and the dryer is in “bound moisture” mode. The wet bulb temperature (adiabatic saturation temperature) is the same as the surface product temperature in a constant drying environment. Once the wet bulb temperature drops, drying is almost complete and the product temperature rises. It helps assure you don’t over-heat the product in the last few zones.
Other Dryers
There are many other industrial dryers including fluid beds (similar physics to spray and flash dryers), Flakt pulp dryers and drum dryers which all can benefit from an accurate exhaust gas humidity measurement. The importance is implementation of the humidity sensor because it is a tool which can provide improved real time process information and control.